.png)
A checklist is a list of items or tasks that need to be completed, reviewed, or verified in order to ensure that a particular process or activity is performed correctly and thoroughly. Checklists are often used in various fields, including aviation, healthcare, construction, and project management, to ensure that important steps are not overlooked and to improve efficiency and accuracy. A well-designed checklist can help reduce errors, increase productivity, and promote consistency in performing tasks.
Benefits of Checklist for organizations-
Checklists can be a useful tool for organizations in many different ways, including:
- Improving efficiency and productivity: By using checklists, employees can ensure that they are completing all necessary tasks in a standardized and systematic manner, reducing the likelihood of errors or omissions. This can help organizations to complete tasks more efficiently and increase productivity.
- Ensuring consistency and quality: Checklists can help to ensure that all tasks are completed to a consistent standard, which can help to maintain quality and avoid errors or oversights.
- Facilitating communication and collaboration: It can help to ensure that all team members are on the same page and working towards the same goals. They can also serve as a communication tool, allowing team members to share information and updates easily.
- Increasing safety and compliance: This tool can be especially useful in industries where safety and compliance are critical, such as healthcare, aviation, construction, pharma, etc. By using checklists to ensure that all necessary safety and regulatory procedures are followed, organizations can help to reduce the risk of accidents or other negative outcomes along with ensuring employee safety.
- Providing a framework for training and development: Checklists can be a useful tool for training new employees or helping existing employees to develop new skills. By breaking down complex tasks into smaller, more manageable steps, checklists can help employees to build their knowledge and confidence over time.
Overall, checklists can be a powerful tool for organizations looking to improve efficiency, consistency, safety, and quality. By implementing checklists in their processes and workflows, organizations can help to ensure that all necessary tasks are completed to a high standard and that all team members are working together effectively.
Introducing Safety checklists
Safety checklists are a tool used by organizations to improve employee safety and reduce the risk of accidents and injuries in the workplace. A safety checklist is a document or form that outlines a series of safety-related items to be checked, inspected, or reviewed.
The purpose of a safety checklist is to ensure that all necessary safety measures are in place and functioning properly before any task or activity is carried out. It is often used as a reminder of the steps or procedures that need to be taken to ensure safety and can help identify any potential hazards or risks that may have been overlooked.
Safety checklists can cover a wide range of safety-related items, depending on the industry and the specific task or activity being carried out. Some examples of items that may be included in a safety checklist are personal protective equipment (PPE) checks, equipment inspections, hazard identification, emergency procedures, and environmental conditions.
Safety checklists are an important part of an organization's safety management system and are often used in conjunction with other safety measures such as training, risk assessments, and incident reporting. An organization can develop them internally or obtain them from external sources such as regulatory bodies or industry associations.
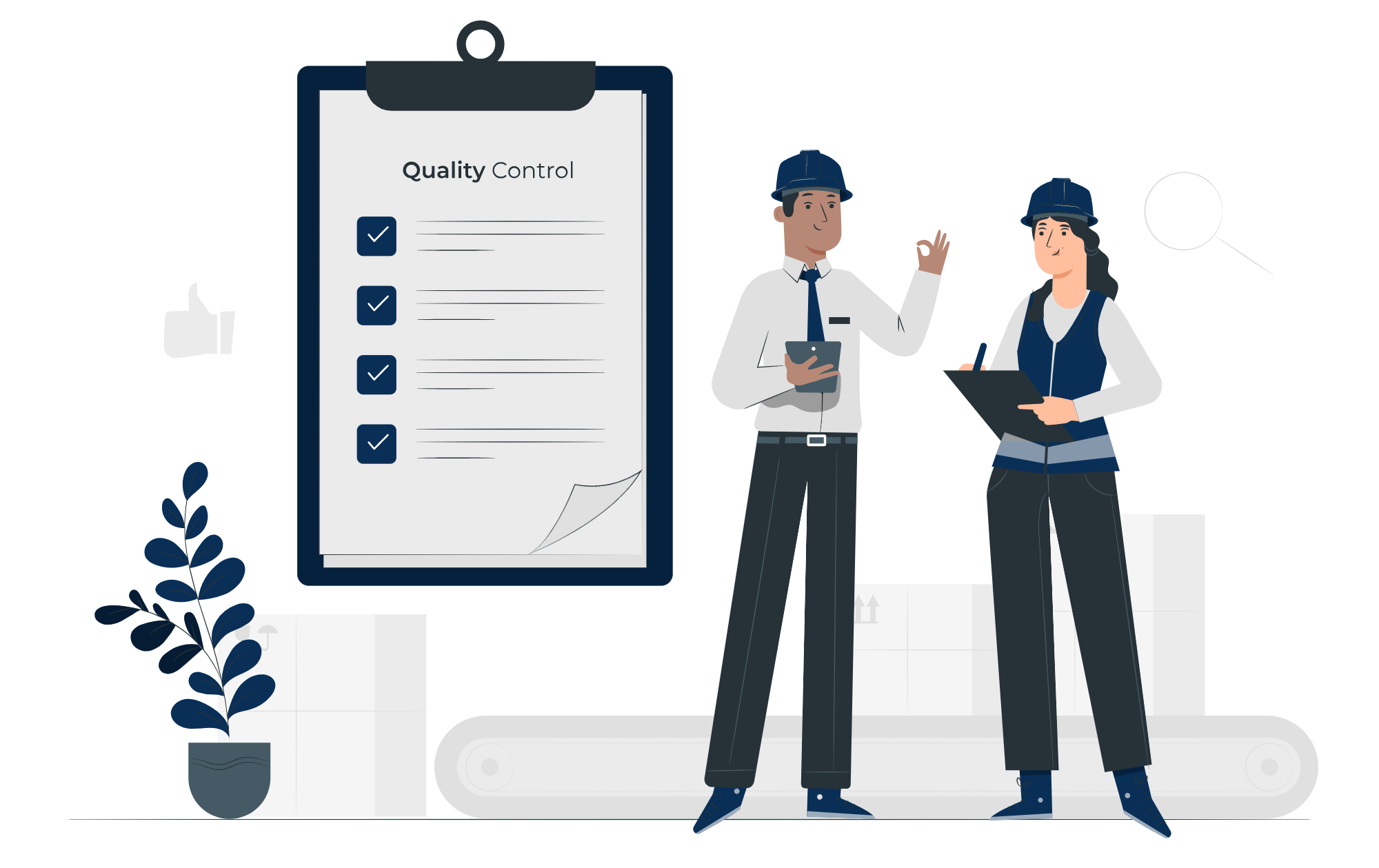
Types of Safety Checklists
There are many types of safety checklists that can be used in a variety of industries and workplaces. Such checklists are proven to improve workplace and employee safety. Here are some common types of safety checklists:
- General Safety Checklists: These are general safety checklists that cover a wide range of safety-related items that may be applicable to most workplaces, such as fire safety, hazard identification, and PPE use.
- Equipment Safety Checklists: These checklists focus on the safety of equipment and machinery, including inspections and maintenance schedules, safety guards, and emergency shut-off procedures.
- Hazardous Material Safety Checklists: These checklists focus on the safety of hazardous materials, including proper storage and handling, labeling, and spill response procedures.
- Vehicle Safety Checklists: These checklists focus on the safety of vehicles, including inspections, maintenance schedules, and safety equipment such as seatbelts, headlights, and brakes.
- Electrical Safety Checklists: These checklists focus on the safety of electrical equipment and systems, including grounding, wiring, and electrical panels.
- Confined Space Safety Checklists: These checklists focus on the safety of confined spaces, including air quality, ventilation, and emergency procedures.
- Workplace Safety Audit Checklists: These checklists are used to perform a comprehensive safety audit of a workplace, including identifying hazards and recommending corrective actions.
- Construction Safety Checklists: These checklists are designed specifically for the construction industry and cover safety-related items such as scaffolding, fall protection, and excavation safety.
- Ergonomics Safety Checklists: These checklists focus on ergonomic issues such as workstation design, lifting techniques, and repetitive motion injuries.
- Emergency Response Checklists: These checklists outline the steps to be taken during an emergency, including evacuation procedures, first aid protocols, and emergency contacts.
Uses/ ROI of checklists for Manufacturing Plants and Field Force
Now that you have a clear picture of safety checklists, let us understand what are its uses, especially for a manufacturing plant and for the field force employees.
- Identifying and Reducing Hazards/Accidents: Safety checklists can help identify potential hazards, such as poorly maintained vehicles or unsafe driving conditions. It can also help employees to evaluate the level of risk associated with each identified hazard. Regular use of safety checklists can help reduce accidents by identifying potential hazards and addressing them before they cause harm.
- Prioritizing safety concerns: The checklist can help prioritize safety concerns based on the level of risk. Employees can use the checklist to develop safety plans to address each safety concern. This course of action is beneficial to ensure employee safety.
- Ensuring compliance: Safety checklists can help ensure that employees are complying with all safety regulations and standards.
- Enhancing communication and teamwork: Safety checklists can improve communication between drivers and their supervisors by providing a structured format for discussing safety concerns. It also encourages teamwork by involving all employees in the identification and resolution of safety concerns.
- Increasing accountability: Safety checklists can increase employee accountability for safety by making them aware of their responsibilities and the consequences of not following safety procedures.
- Improving productivity: A safe driving environment can improve productivity by reducing the amount of time employees need to take off work due to accidents. The same logic applies to a manufacturing plant as well.
- Reducing vehicle maintenance costs: Safety checklists can help identify potential issues with vehicles before they become major problems, reducing the cost of maintenance.
- Mitigating legal liability: Regular use of safety checklists can help mitigate legal liability in the event of an accident.
- Demonstrating commitment to safety: The use of safety checklists demonstrates a company's commitment to employee safety, which can improve employee morale and retention. A strong commitment to safety can enhance a company's reputation as a responsible and trustworthy organization. Customers are more likely to be satisfied with a company that prioritizes safety, which can lead to increased business and referrals.
- Reducing absenteeism: A safe driving environment can reduce the amount of time employees need to take off work due to accidents or injuries.
.png)
How Does SafetyConnect Help?
SafetyConnect, an AI-Powered Driving Safety Solution, helps enterprises to analyze the at-risk driving behavior of field employees. You can enhance the driving safety of these employees with SafetyConnect. This application enables you to ensure that all necessary vehicle and pre-trip inspections are carried out, with its Checklist feature. Enterprises have the autonomy to decide what kind of checklist will be incorporated to improve driving safety, productivity, and efficient deployment of tasks. You can request a demo here.